Hydraulic Basics: Sequencing Multiple Cylinders (Actuators)
1. Introduction
In pneumatic or hydraulic system, we can defined the motion of two or more cylinders by placing and linking the sensors to the actuating mechanism. In this blog, we create a circuit that sequences the extending and retracting of two double-acting cylinder. Also, we discussed the process involve in details.
Similar to the previous blogs, we used a scenario or a problem that serve as the basis for our circuit. In this blog, we define the problem as
Boxes are moved from a vertical stack into a conveyor. Cylinder A pushed the boxes from the stack and Cylinder B transfers the box to the conveyor. Cylinder A retracts at after the box is push into the conveyor while cylinder B retracts after cylinder A returns to initial state. The process is activated by pressing a button. To confirm the cylinder position at any given time, a pair of limit switch is placed in each cylinder.
To elaborate the problem, we used two cylinders to fulfill the process requirement. The motion of the cylinders are A+, B+, A-, and B-. The plus sign (+) indicates the cylinder is extended while the minus sign (-) means cylinder retracts. The motion sequence stated earlier is our guide in placing and linking the sensors. In the next section, we show the circuit and discussed in details.
2. Circuit and Simulation
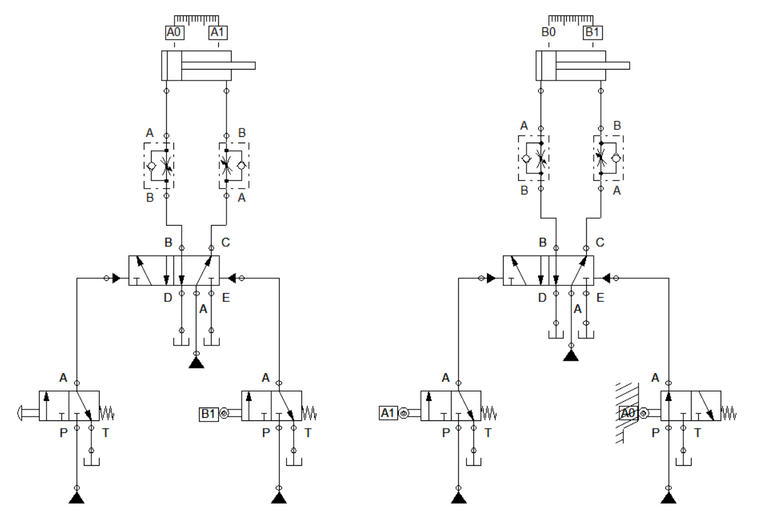
Figure 1: Hydraulic Circuit for Sequencing Multiple Cylinders
The hydraulic circuit shown in Figure 1 displays the connections of the different components for the scenario at hand. Each cylinder is driven by a pair of manually or mechanically actuated 3/2 way directional valve, a hydraulically actuated 5/2 way directional valve, and a pair of flow control valve. At cylinder A, The 5/2 way DCV is driven by a 3/2 way DCV with push button and a 3/2 way DCV with limit switch. The limit switch serves as the sensor that detects when is the cylinder to be retracted. On the other hand, cylinder B is driven by a pair of 3/2 way DCV with limit switches. The one-way flow control valve is placed to reduced the speed of the cylinders.
The sensors A0, A1, B0, and B1 is linked to the 3/2 way valves in accordance to the motion sequence define in section 1. A0 and B0 are placed at the full retracted length of the cylinder while A1 and B1 is placed at full extended length. At cylinder A, sensor B1 is linked to the retraction of the cylinder so that it retracts after cylinder B completed the task. This enables the A- in the sequence to activate. For cylinder B, A0 and A1 are linked to its 3/2 way DCV. A1 is linked to the extending motion of the cylinder. This is to assure that cylinder B extends after cylinder A fully extended. A0 is placed at retracting motion of cylinder B so that cylinder B retracts after cylinder A. This placement of sensors enables A+, B+, A- and B- to be accomplished.
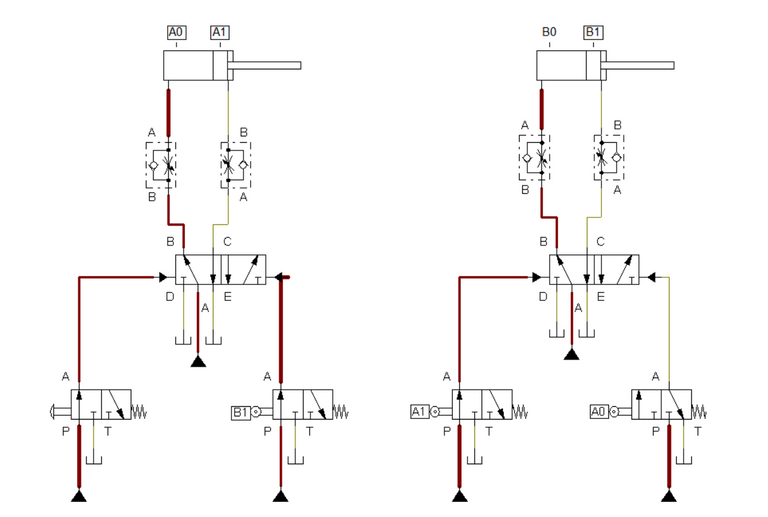
Figure 2: Push button is pressed.
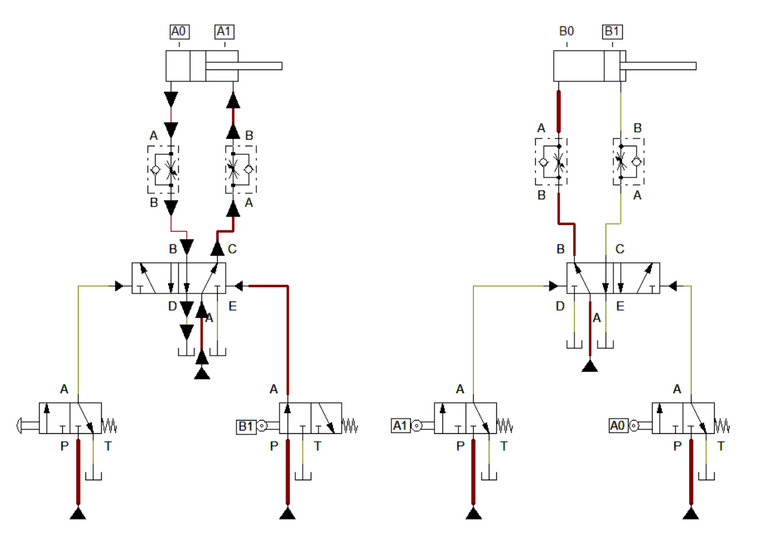
Figure 3. Cylinder A retracts after Cylinder B reaches sensor B1.
When the push button is pressed, 5/2 way DCV at cylinder A opens port B to actuate cylinder A. This extends cylinder A. As cylinder A reached sensor A1, sensor A1 transmit a signal to open port B at 5/2 way DCV of cylinder B. The cylinder B extends and reaches sensor B1. Sensor B1 send a signal to retract cylinder A. Cylinder A returns to initial state and sensor A0 is activated. This result to cylinder B return to initial condition. The animated simulation is shown in Figure 4.
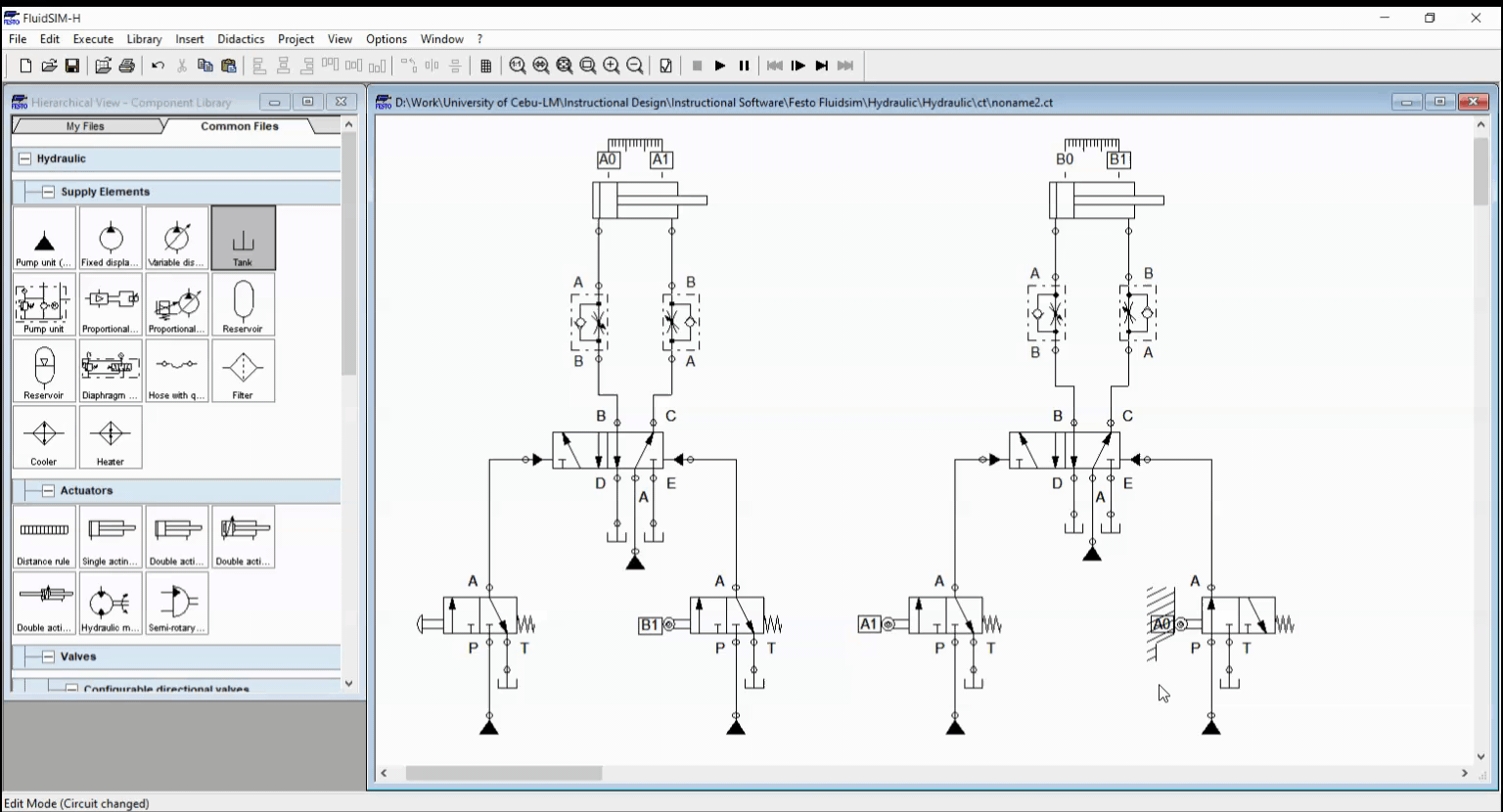
Figure 4: Full Simulation
3. Conclusion
In this blog, we discussed on how we correctly assigned the sensors of multiple actuators and operates a hydraulic circuit consisting of multiple cylinders. The placement of each sensors dictates the motion of the cylinders connected in the circuit. When signals from the sensors overlaps, the motion or the process is interrupted due to incorrect assignment of sensors. In the this blog, we used limit switches but in a practical setting, there are variety of sensors that can be used. Fully understanding the sequence of motion or the process itself aids in correctly assigning the sensors across the circuit.
4. References
[1] Hydraulic Basic Level. online access
[2] Hydraulic Advance Level. online access
(Note: All images and diagram in the text are drawn by the author (@juecoree) except those with separate citation.)
Hello Hive! If your are interested in pneumatic and hydraulic series, you can read:
Pneumatic and Electro-pneumatic
1. Pneumatic Basics: Direct Control
2. Pneumatic Basics: Indirect Control
3. Pneumatic Basics: AND and OR Logic
4. Pneumatic Basics: Memory Circuit and Speed Control
5. Pneumatic Basics: Dependent control
6. Pneumatic Basics: Multiple Actuators
7. Electro-pneumatic Basic: AND and OR Logic
8. Electro-pneumatic Basics: Interlocking, Latching and XOR logic
9. Electro-pneumatic Basics: Distribution of Workpiece
10. Electro-pneumatic Basic: Ejecting a workpiece
11. Electro-pneumatic Basics: Basic Automation
12. Electro-pneumatic Basics: Automation with Counter
12. Electro-pneumatic Basics: Automating with Timer
13. Electro-pneumatic Basics: Cementing Press (Time Dependent Control)
14. Electro-pneumatic Basics: Embossing Device
15. Electro-pneumatic Basics: Bending Device
16. Electro-pneumatic Basics: Introduction to Logic Module
17. Electro-pneumatic Basics: Automating with Logic Controller
18. Electro-pneumatic Basics: Logic Controller for Multiple Actuators
19.Electro-pneumatic Basics: Time-dependent control with Logic Controller.
Hydraulics
20. Hydraulic Basics: Direct Control
21. Hydraulic Basics: Indirect Control
22. Hydraulic Basics: Dual Pressure Value and the AND Logic
23. Hydraulic Basics: Shuttle Valve and the OR Logic
Posted with STEMGeeks