Understanding the Input and Output of a Control System
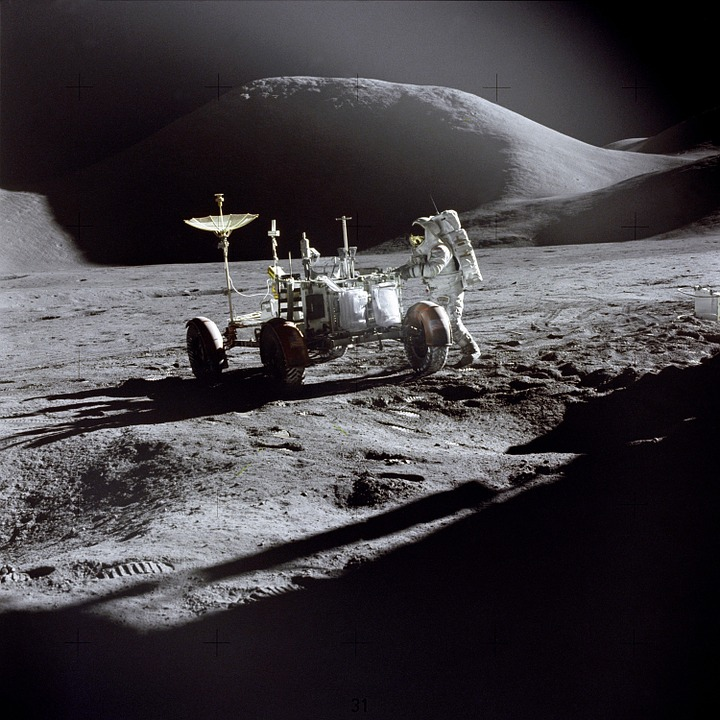
image source
Introduction
Technology enables us to quickly adopt new methods and use it to make effective control systems for various automated processes. We are capable builders of automated systems. These systems are efficient and low-cost, which raises the capability to manufacture products effectively. Process automation are adapted by almost all industries and it has been successful to optimize processes.
The core of process automation is a well-design control system. A control system involves simple and complex integration of devices to achieve and optimize a certain task. In engineering, the term "control" implies effective and optimize guidance or manipulation of process or system environment with less errors. For example, it could be regulating your room temperature to stay at 21 degree Celsius; or, as complex as maneuvering a space shuttle or a seagoing vessel.
To build the complex control system mechanism, we need to study different variables that are involve in a specific processes. An effective control is build to effectively run the process or system with high capability to adapt and regulate failing conditions. Today, there are more complex and integrated systems in place.
To be able to develop an effective control system, we start by defining a system. A system is any set of objects which interconnected to perform a certain task. Earlier, I already define the term control. It means to direct or force a system to a predetermine specific values. So, by understanding both term's definition, control system is any set of objects which is interconnected to direct or force a system to your desired specific values.
Control system bridges our desired preferences to the actual response of the system. In understanding the behavior of control system, we must identify different variables. An important variables need to be identified properly are inputs and outputs.
Identifying Input and Output
Input are actions or stimulants rather than the raw materials or variables. These actions enables the system to response accordingly. In a control system, input are either setting a desired values or actions that stimulate the system to do a specific task. In contrast, outputs are the actual result or response in a control system.
For example, I want to maintain my room temperature to 20 degree Celsius. So, I need to set the air conditioning unit to a 20 degree Celsius. My act of setting the air conditioning unit to 20 degree Celsius is the input. The output is the actual temperature that can be measured in my room. So, inputs are actions that leads to your desired output. On the other hand, outputs are the actual response in reference to the input. However, in reality, actual response(output) deviate from the desired response (input).
Let have another example. I want to toast a bread on an oven toaster for 3 mins. So, what is the input and output in the system? When I set the timer to 3 mins, I was able to guide the toaster to toast the bread within 3 mins. So, the act of setting the timer to 3 mins is the input. A actual toasted bread after 3 mins is the output.
Independent, Dependent and Manipulated Variable
In toasting the bread, the toasting time is dependent on my desire to set the timer. Each time I set the timer to a different time. A different toast is achieved. My preference of setting the timer is independent to the oven toaster system.
My actual toasted bread is dependent on the time I set on the oven toaster. The setting of the timer is an independent variable on the system. It means that the system does not affect my decision to set the timer. In contrary, the actual toasted bread is dependent on the time set on the oven toaster. So, the actual toasted bread is a dependent variable on the system.
Another variable in the control system is the manipulated variable. In the earlier example, as the oven timer is set to 3 mins, heat start flowing and circulating inside the oven toaster. After 3 mins, the heat flowing through the oven toaster is cut off. The heat flowing through the oven which cause the toasting of the bread is the manipulated by the setting on the timer. Heat flows when the we start toasting; and, heat flowing is cut off when toasting time is done.
Let us have another example. A faucet valve is an example of a simple control system. When I desired to let the water flow, I need to open the valve. We already know earlier that the actions that leads to a result or a response in a control system is an input. So, the act of turning on the valve is the input, and its is an independent variable. The percentage of opening the valve is dependent on my desires of the amount of water flowing on the faucet. In addition, the actual flow of water is the output (dependent variable). A different percentage of opening the value results to different rates of flow in the water coming out the faucet. So, the rate of flowing is the manipulated variable.
Another example is a drain valve of a tank. When I desired to let the water flow, I need to open the valve. We already know earlier that the actions that leads to a result or a response in a control system is an input. So, the act of turning on the valve is the input, and its is an independent variable. The percentage of opening the valve is dependent on my desires of the amount of water flowing on the faucet. In addition, the level of water is the output (dependent variable). A different percentage of opening the value results to different rates of flow in the water coming out the faucet. So, the rate of flowing is the manipulated variable.
Open-loop and Closed-loop System
We classify control system either open-loop or closed-loop system. The oven toaster scenario earlier is an example of an open-loop system. The input is dependent to an operator. It is also called as manually-operated control system. For example, in the oven toaster scenario, I was assuming to set the oven to 3 mins to have a toasted bread. The input is dependent on my preference. The output is not assured to have a perfect toast. The users preferences dictates the time of toasting instead of having a well toasted bread all the time. It causes different outcomes at any action taken by an independent operator. Typically, the resulting quality of the toasted bread is not controlled. So, there is a chance that the operator need to adjust the input. It is not scalable due to its dependence to an operator.
In open-loop system, the system does not give a feedback whether the output is already attained. It is solely dependent on the human operator. In contrast, closed-loop system gives a feedback in reference to the output. It automatically adjust the input to suit the desired actual response in the system. Usually, closed-loop system employs sensors that detects and transmit the information from the output to the controller. Thus, closed-loop system is also known as automatic feedback control system.
For example, in the oven toaster example earlier, the oven toaster is an example of an open-loop system. So, the users decides the quality of the toasted bread. In a closed-loop system, it should be the system has the capability to assess if a perfect toast is already achieved. It is done by adding a sensor that detect the color of the toasted bread.
In an closed-loop system, instead of setting a time as an input, I would set that a perfect toasted bread is golden brown. So, the control system allows heat to flow into the oven until the sensor detects that the toasted bread is already golden brown. In such event, the bread automatically comes out from the toaster.
Closed-loop system efficiently achieved the desired response of a system without relying on the judgement of a human operator. The sensor effectively detects the condition of the system. It send out signals to adjust the manipulated variable to suit the present condition of the system.
In closed-loop system, the actual response is always compared to the input reference. The input reference is called the setpoint. The errors between the desired and actual response is called an offset.
In open-loop system, the operator detects the error and make the necessary adjustment in the controller. It is a disadvantage of the open-loop system. Open-loop system is prone to errors including external effects. Open-loop system does not recognize errors from the output. It only perform what was set on its input regardless if the input could be achieved.
Closed-loop system has eliminate this disadvantage by employing a sensor and a feedback loop. The system can automatically adjust the input in accordance to the its actual response. Errors in closed loop systems are minimal.
Final Thoughts
Control system is any set of objects interconnected to guide or force another system to a predetermine specific value. In control system, input is any response or action desired to be produced in a system. The reference input is called setpoint. On the other hand, output is the actual response of the system.
We discuss different examples to identify the input and output of a control system. One example scenario is about an oven toaster. The setting of the timer was identified as the input. The output is the actual toasted bread.
We have also identified different variables in a control system. There are independent, dependent, and manipulated variable. Using an example, we have associated these variables to a control system. Independent variables refers to the input or reference of the system. These parameters are not affected by the control system. In contrary, dependent variables are solely dependent to the input of the control system. Typically, these are the output of a system. Manipulated variables are parameters that are controlled to produce the desired output.
Furthermore, we have discuss about open-loop and closed-loop system. Open-loop system does not monitor the output of the system. In open-loop, there is no feedback loop. So, the input is solely dependent on the operators judgement and decision on the actual response of the system. It is more likely to have errors. Open-loop system is also called as manually-operated control system. In contrary, closed-loop system has a feedback loop. So, it has the capability to compare the desired and actual response of the system. Closed-loop employs sensors to monitor and measure the actual response of the system. Lastly, It automatically adjust the system to achieved the desired response.
References
Images
All images in the blog is created and edited by the author except those with citation. Vectors in the images are download from Freepik, which has a stack of free to use stack vector and photo.
https://twitter.com/juecoree/status/1359859598002319362
Thanks for your contribution to the STEMsocial community. Feel free to join us on discord to get to know the rest of us!
Please consider supporting our funding proposal, approving our witness (@stem.witness) or delegating to the @stemsocial account (for some ROI).
Please consider using the STEMsocial app app and including @stemsocial as a beneficiary to get a stronger support.